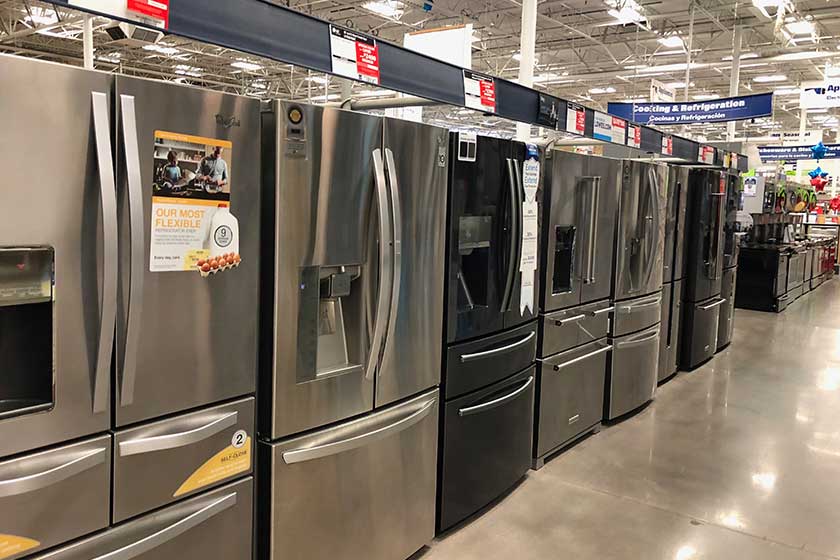
Meeting Lowe’s RFID requirements is a strategy for success in the current retail supply chain. Lowe’s has set a high bar for its suppliers by rolling out a new RFID program following compliance with industry standards for RFID tagging and serialization to keep their operations smooth.
Lowe’s new RFID requirements aim to improve inventory accuracy, enhance supply chain visibility, and create better customer shopping experiences. RFID tagging brings precision to retail operations. However, achieving compliance with Lowe’s standards involves planning, the right partnerships, and flawless execution. Suppliers must adhere to GS1 RFID serialized encoding standards and use Auburn University’s ARC-approved inlays.
Compliance is an important part of doing business with one of the largest home improvement retailers. Let’s break down what you need to know and do to meet Lowe’s requirements.
Understanding Lowe’s Vendor Requirements for RFID
Meeting Lowe’s vendor requirements for RFID compliance covers every aspect of RFID implementation, from inlay specifications to tag placement. Lowe’s expects its suppliers to use RFID technology for specific merchandise divisions such as appliances, hardware, and apparel items. To meet these expectations, suppliers must use industry-specific standards that promote efficiency and scalability.
The Role of ARC-Approved Inlays in Lowe’s Standards
One key component of compliance is selecting ARC-approved inlays. Auburn University’s RFID Lab rigorously tests these inlays for performance and Lowe’s mandates specific inlay performance for each product group.
For instance, manufacturers require Y2-spec inlays for appliances. These specifications guarantee that RFID tags perform reliably, even under challenging conditions like metallic packaging or different product shapes.
After selecting the appropriate inlay, suppliers must submit samples for validation through Auburn University’s ALEC program. This validation confirms that the tags meet performance benchmarks and data requirements before mass production begins.
Tag Placement Standards for Maximum Readability
Proper tag placement is central to maintaining RFID readability across various supply chain stages. Lowe’s has adopted guidelines from Auburn University’s RFID Lab to specify tag positioning. Various product types and packaging formats determine a tag’s position.
For example, tags for appliances should avoid direct contact with metallic surfaces to prevent signal interference. Meanwhile RFID tags for clothing and workwear must be attached without obstructing branding or compliance labels.
Suppliers can consult Auburn University’s resources or contact their support team if a product category lacks specific tag placement instructions. Incorrect placement can result in unreadable tags. This may disrupt inventory accuracy and cause operational delays.
GS1 Standards and Unique Serialization Requirements
All RFID tags must comply with GS1 standards for encoding and serialization. These standards involve encoding unique identifiers, such as SGTIN-96, into each tag to distinguish individual items. This level of granularity eliminates the risk of duplicate serial numbers, which can create confusion in Lowe’s inventory systems.
Quality Assurance Before Bulk Production
Before suppliers begin mass-producing RFID-tagged products, Lowe’s requires them to undergo a quality assurance process through Auburn University’s ALEC program. Vendors must submit five production-quality tag samples for validation. They come with specific instructions depending on the product category and packaging format. Suppliers can proceed with large-scale production only after ALEC approves their request.
This process includes testing RFID tags for readability and performance. The testing simulates real-world conditions like sales floors and distribution centers. Suppliers must address the issues if tags fail to meet standards during validation and resubmit for approval.
Adapting to Specialty Tagging Scenarios
Certain products require different RFID tagging solutions. This includes products such as patio furniture sets or grills. For items sold as sets but packaged in multiple boxes, only one box should carry the RFID tag. Suppliers must consult Auburn University’s RFID Lab for specialized cases.
Products with materials like metal, foil, or glass also require tags that minimize interference. Suppliers must work with RFID experts to select the appropriate tags. Then, they can determine placements that provide readability without affecting performance.
Auburn University provides specific recommendations for such challenges. They can assist suppliers to achieve compliance efficiently.
The Role of RFID Technology in Lowe’s Supply Chain
RFID technology improves Lowe’s inventory tracking by providing real-time visibility. Suppliers can read these RFID tags automatically, unlike traditional barcode systems that require manual scanning. They even work when items are not in the direct line of sight. This function allows Lowe’s to monitor inventory levels accurately and respond quickly to demand fluctuations. Ultimately, it results in fewer stockouts, faster replenishment cycles, and improved supplier order fulfillment rates.
The precision of RFID tagging enables Lowe’s to maintain high inventory accuracy in its warehouses and retail locations. Embedding tags into product packaging enables suppliers to track the movement of goods. This creates an ecosystem where every step is accounted for.
It reduces the risk of shrinkage through theft, damage, or administrative errors. This technology improves Lowe’s customer satisfaction by making sure products are available when needed.
Addressing Tag Interference Challenges
One of the most common challenges with RFID technology is signal interference. Metals, liquids, and packaging materials can reflect or absorb RFID signals. Interference can compromise tag readability and lead to errors in inventory tracking.
For example, appliances or plumbing fixtures often contain metal components that can disrupt signal transmission. Suppliers must consider these factors during the tagging process.
The solution lies in careful tag placement and selecting RFID tags for difficult environments. Position the tags to minimize interference. Avoid direct contact with metal or placing tags on non-conductive surfaces. Suppliers can reference resources like Auburn University’s tag placement guidelines to identify best practices for different product categories.
Optimizing Tagging for Retail and Warehouse Environments
RFID tagging must account for the diverse environments in Lowe’s supply chain. These facilities include warehouses, distribution centers, and retail stores. Each environment presents challenges suppliers must address to maintain tag performance.
For instance, warehouse tags must remain readable when products are stacked or stored on metal shelves. Similarly, tags must be positioned properly for quick scanning on retail shelves.
Using durable, high-quality RFID labels and tags is essential to withstand handling, environmental factors, and long-term storage.
The Role of RFID in Shrinkage Reduction
Shrinkage remains a significant issue in retail. RFID reduces losses due to theft, misplaced inventory, or discrepancies in stock counts. It does so by tracking items at the individual level. RFID tags allow retailers like Lowe’s to track shrink at the item level with dynamic visibility, pinpointing losses by store. These insights help replenish missing inventory to ensure a positive customer experience and enable targeted loss prevention measures to minimize shrinkage in their stores.
Utilizing Advanced RFID Labels for Compliance
Using the wrong RFID label can lead to compliance failures or operational inefficiencies. Lowe’s requires tags that meet specific ARC inlay standards for each product category. Partnering with an expert in RFID technology and implementation simplifies this process. Providers of advanced RFID solutions offer labels for specific product needs, from apparel to heavy-duty appliances. These labels are durable and designed to integrate into your existing packaging workflows.
The RFID Compliance Process
Lowe’s vendors must confirm that their RFID tags meet Lowe’s performance criteria and will function correctly within the retail environment. Quality checks are mandatory. Suppliers must verify that tags are encoded correctly and perform as expected. This includes checking tags in real-world scenarios, such as reading them at the factory, the DC, and in-stores.
Staying Ahead with RFID Innovations
RFID technology is no longer a tool limited to inventory tracking. Its continuous development has introduced advanced functionalities that significantly enhance operational efficiency. Innovations like automated inbound audits eliminate manual scanning.
RFID technology provides instant updates on stock levels and enables proactive restocking. This means better demand forecasting and improved resource allocation for suppliers. Such capabilities align perfectly with Lowe’s focus on efficiency and customer satisfaction.
Partnering with FineLine Technologies, Inc. for RFID Compliance
Meeting Lowe’s RFID requirements doesn’t have to be a challenge. At FineLine Technologies, Inc., we help suppliers manage every aspect of compliance, from inlay selection to data serialization. We engineer our RFID labels for durability and performance.
We provide customers with the first RFID quality control application on the market to simplify the RFID quality control process. Our app, QCtrak, is designed for manufacturers to ensure their products are correctly RFID tagged and meet retailer’s requirements.
Meanwhile, our FASTtrak platform guarantees high-quality RFID tags and labels with a 48-hour turnaround time. This speed and reliability help you ensure compliance and avoid delays and penalties.
Confidently meet Lowe’s requirements with our support. Contact us today to ease your RFID implementation and take your business to the next level.