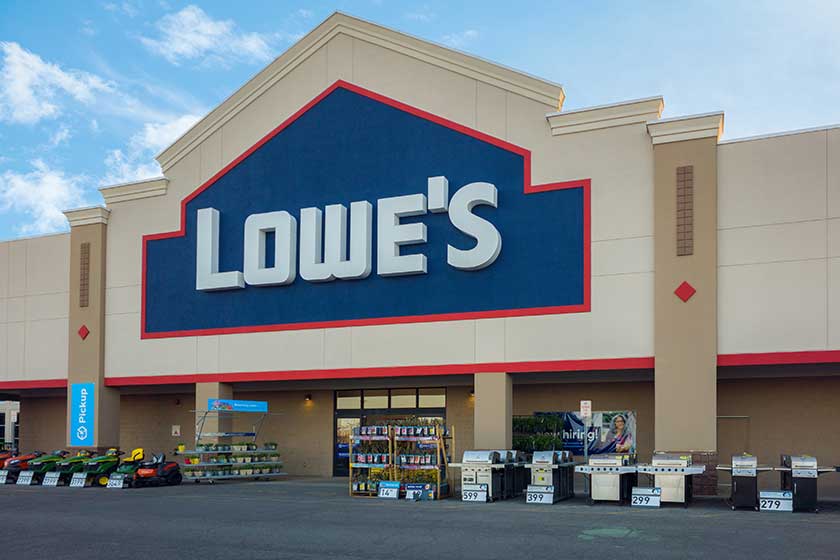
Lowe’s recent initiative requiring RFID tagging on items in specific departments marks a significant shift in retail operations. As the home improvement retailer rolls out this program nationwide, it’s crucial to understand the implications of these changes. This post explores Lowe’s RFID initiative, its effects on suppliers, and how to ensure your business is prepared.
Understanding Lowe’s RFID Initiative
Lowe’s, like other major retailers, is adopting RFID technology to improve inventory management, increase the accuracy of stock levels, and streamline the supply chain. By implementing RFID, Lowe’s aims to reduce stockouts, improve product availability, and ensure that products are always in the right place at the right time—enhancing the overall customer experience.
As part of its RFID mandate, Lowe’s expects vendors to adhere to established industry standards, such as the GS1 encoding standard, Auburn University RFID Lab tag placement guidelines, and ARC inlay standards. All products must meet these standards before arriving in stores. Vendors are also expected to perform quality checks to ensure there are no duplicate serial numbers and that each tag is correctly encoded for the specific item it is attached to.
How are Vendors and Manufacturers Affected?
- Impact on Supply Chain Processes
Lowe’s RFID initiative is expected to set a new standard in the retail industry, with the potential for ripple effects from other large retailers. Vendors and manufacturers producing or distributing products for Lowe’s will need to modify their processes to incorporate RFID tags. This may involve new investments in technology, employee training, and adjustments to ensure compliance with Lowe’s RFID specifications.
- Compliance and Quality Control
Vendors will be required to implement quality control measures to ensure that every RFID tag is unique, properly encoded, and complies with Lowe’s standards. This could involve additional training for staff and new quality assurance processes to verify that there are no duplicate serial numbers and that the tags are correctly encoded for each product.
Benefits of RFID in the Retail Industry
- Enhanced Security and Loss Prevention
RFID technology helps reduce shrinkage by providing better tracking and more accurate records. This can minimize losses due to theft, misplacement, or errors in inventory management.
- Improved Inventory Accuracy
RFID provides real-time visibility into inventory levels, allowing both suppliers and retailers to track products more accurately throughout the supply chain. This leads to better stock management, reducing issues like stockouts or overstocking, and ensures that products are always in the right place.
- Better Supply Chain Visibility
RFID enhances end-to-end visibility of products as they move through the supply chain. Suppliers and retailers can track product locations in real-time, identify bottlenecks, and improve forecasting and planning, ultimately leading to smoother operations
How to Prepare for the Future of RFID
Here are a few steps businesses can take to prepare for Lowe’s RFID initiative and the growing role of RFID technology in the industry:
- Evaluate Existing Technology
Assess current inventory and inventory data collection systems to determine if they are compatible with RFID technology. Upgrading systems now can prevent disruptions as RFID becomes more widespread in the retail industry.
- Collaborate with Supply Chain Partners
Work closely with an approved packaging supplier to ensure RFID tags meet the required standards and are properly applied or embedded during the manufacturing process. This collaboration will help optimize your operations and ensure smoother compliance with retailer mandates.
- Train Employees
Invest in training programs to help employees understand how to manage and use RFID systems effectively. A knowledgeable staff will be better equipped to support customers and ensure a seamless transition to RFID-enabled processes.
RFID Compliance: What’s Next for Your Business?
With Lowe’s RFID mandate underway, vendors need to remain informed and involved if they want to prevent disruptions. It’s essential to work with a trusted provider like FineLine to guarantee you are equipped with the right RFID labels, tags, and packaging to meet Lowe’s compliance standards.
Partnering with us gives you access to industry-leading solutions that support both your immediate compliance needs and your long-term operational goals. RFID is not only a response to Lowe’s requirements but also a transformative technology that will help your business improve accuracy, reduce errors, and increase efficiency.
With FineLine’s expertise and advanced technology, you can guarantee a smooth transition and take advantage of the many benefits RFID offers over traditional barcode systems. If you’re ready to get started or need assistance with your RFID label requirements, contact us today. We’re here to help your business stay ahead.